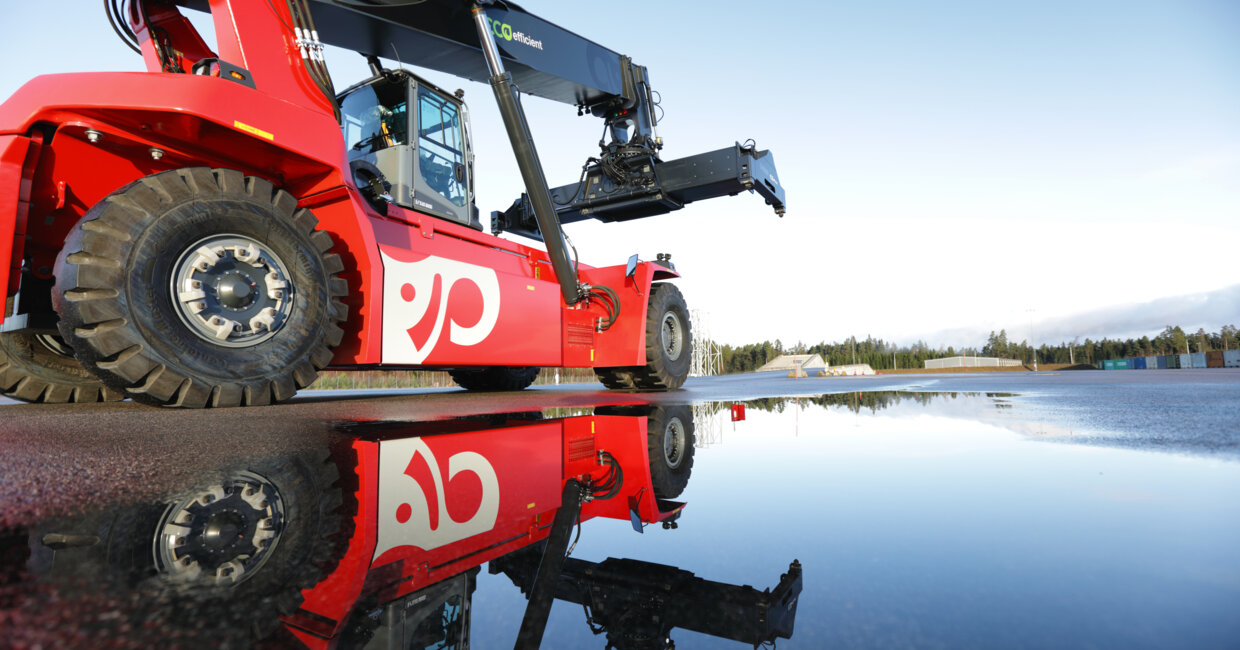
Towards eco-efficient cargo handling operations, part 3: Evaluating available solutions
In this article series, we examine Kalmar's recommended step-by-step approach to eco-efficient cargo handling operations. In part 3, we discuss some of the specific equipment choices that are available to terminals now and in the future.
Today's cargo handling solutions are becoming greener, and most importantly, eco-efficient – meaning they enable operations that are more sustainable without sacrificing productivity or efficiency. Zero-emission equipment is being adopted widely for both on-road and off-road equipment and vehicles. In terminal operations, the first machines to be electrified have been light lift machines such as forklifts, but electrification has progressed steadily to medium and heavy container handling equipment.
Kalmar is leading this development, and in 2021 the company introduced a full range of electric mobile cargo handling equipment, complementing its existing electric machines with the next generation of all-electric reachstackers, heavy forklifts and terminal tractors. As zero-emissions technology matures throughout the industry, economies of scale will lower deployment costs and boost further market demand, driving progress towards fully sustainable logistics.
"When designing eco-efficient container handling solutions, equipment choices always go hand in hand with the overall infrastructure design of the terminal," says Mette Kjems Baerentzen, Product Portfolio Manager, Counterbalanced Container Handlers, Kalmar. "What kind of productivity do you need for your operation, and what kind of fleet does it require? From there, we can move to the specifics of charging management, power grid capacity and other factors. It's all about balancing what is available with what you need to accomplish."
Small design changes, major impact
Equipment emissions are a natural focus when talking about eco-efficiency, but the full picture is more complex. Eco-efficiency is about using the smallest possible amount of energy with minimum impact on the environment while maintaining, or even improving, performance and efficiency. This is not an easy equation, but there are several ways to solve it, once a company has an overall vision and targets toward which it can work.
Eco-efficient powertrains can deliver the most energy-efficient solutions for cargo handling, either by using one of the several currently available battery technologies, or utilising hydrogen in fuel cell based powertrains. Productivity-adapted smart energy solutions use different power settings according to the performance that is needed at any given time. If maximum throughput is not needed, driving and lifting can be done slower to save energy.
Lightweight design with high-strength materials can make heavy equipment lighter, reducing energy consumption as well as tire wear. Finally, regenerative energy accumulation can utilize braking and load lowering as energy sources, reducing external power consumption.
"When designing eco-efficient container handling solutions, equipment choices always go hand in hand with the overall infrastructure design of the terminal."
Driven by data
Electric cargo handling equipment needs batteries that can be based on either Lead-Acid or Li-Ion chemistry, which have different charging and handling requirements. The choice of solution needs to be based on the current operations and expected future business of the terminal. How many opportunity charging possibilities does the fleet have during the day? How many non-stop hours does the equipment need to operate? These and many other factors need to be known in order to design the solution correctly.
A common concern at terminals is how electrification will impact productivity, since electric equipment needs to be charged more often diesel-powered machines are refuelled. However, today’s reachstackers around the globe spend an average of 30% their time idling, with almost half of all running hours consisting of 25% to 45% idling.
Example calculations can easily demonstrate the feasibility of integrating opportunity charging into existing drive cycles and operational schedules. For example, an electric reachstacker with an average driving load and a small-to medium-sized battery with 300 kW charging can easily be powered for a full day shift by opportunity charging during two 15-minute coffee breaks and a half-hour lunch break, provided the charging station is located close to the employee facilities.
"Collecting accurate real-world data is the key to succeeding in this transition to all-electric," notes Mikael Andersson, Product Manager, Kalmar Forklift Trucks & Container Toploaders. "It's important to note that when we move from electrifying smaller forklifts to heavy container handling equipment, we are shifting the focus from lightweight auxiliary equipment to the core of the terminal's business. As a result, we need a much more detailed evaluation of the whole fleet and the operations of the customer."
Long-term capacity
A key part of electric cargo handling equipment is the battery, which also constitutes a significant portion of the equipment investment. Depending on usage, Li-Ion batteries can easily have a first life of 10 to 15 years, which ensures good residual value and return on investment. After this, the battery will still have a lot of capacity left, so it can be reused either in other equipment or repurposed for local energy storage.
Once there is no more financially viable repurposable life in the battery, it will be recycled and the materials might become part of a new battery. This means that the overall sustainability level of a Li-Ion battery solution is very high.
"Battery technology is developing extremely fast," notes Niclas Samuelsson, Product Manager, Terminal Tractors, Kalmar. "Every year, we can get more power for a given cost, so we are starting to see that the battery-powered concept can cover even equipment with very demanding usage requirements. As an industry, we are only just beginning the electrification of heavy container handling machines, but have already reached the point where zero-emissions equipment has the potential to support every step in the container handling process."
"Collecting accurate real-world data is the key to succeeding in this transition to all-electric."
Lifetime value
Selecting the best eco-efficient solution is a complex decision that needs to be based on the overall goals and long-term business plan of the terminal. Factors to be considered range from operational requirements to local regulations and total cost of ownership calculations. Does the terminal need to run one, two or three shifts per day? Are noise levels in urban areas a key consideration? What are the cost differences in purchasing price versus operational costs for the projected ownership time, taking into account the lower service and maintenance costs for batteries and electric motors compared to traditional diesel drivelines?
And finally, which equipment will help the terminal reach its sustainability and productivity targets as soon as possible?
"It's always important to keep an eye on the big picture," says Mette Kjems Baerentzen. "Energy efficiency is the key to electric solutions, so you want to optimise the charging system for your equipment, while simultaneously making the best use of new design possibilities. Finally, you need data and fleet management to see how you can continuously improve your performance. The great thing is that focusing on energy efficiency can also lead to productivity gains, but for this to happen you need the data and insights from your own operations."
Related articles
Subscribe and receive updates in your email
Suscríbase a nuestras publicaciones